Environmental
Pollution mitigation
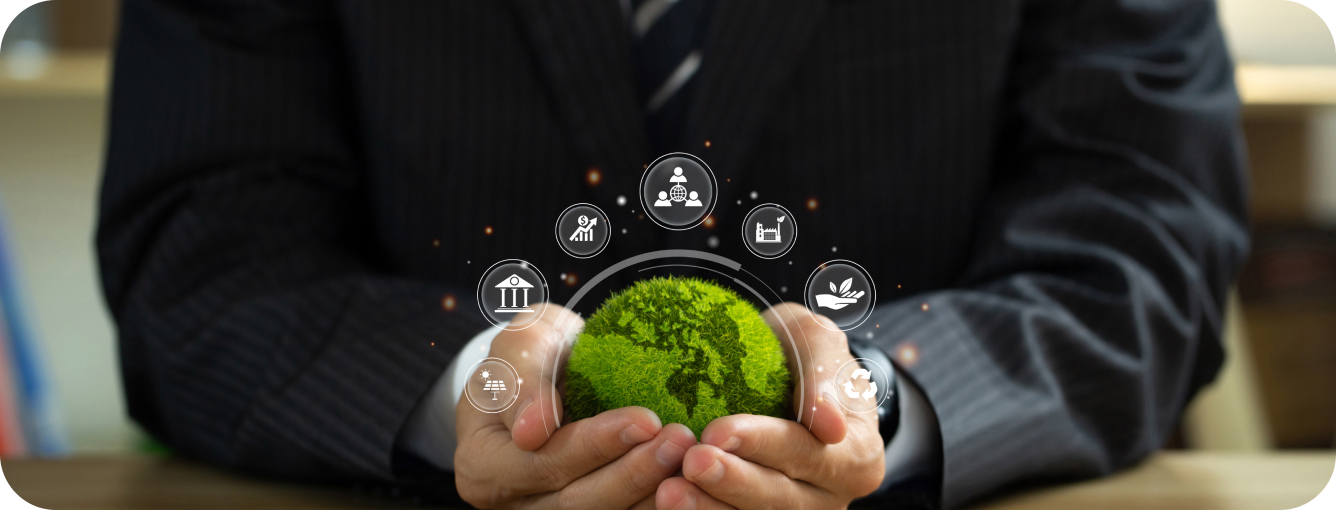
Pollution Prevention
-
Environmental Regulatory Compliance Principles
Hyosung TNC adheres to the following principles to minimize environmental pollution, manage environmental risks efficiently, and comply with environmental regulations through a comprehensive approach:
1We immediately incorporate amendments to environmental regulations based on our environmental management policy, manuals, and processes. We meticulously review environmental regulations and evaluate compliance annually.
2We strive to minimize environmental impacts by establishing internal standards that are more stringent than legal requirements.
3We transparently communicate our compliance with an environmental regulations to stakeholders through various channels, such as sustainable management reports, environmental information disclosure systems, and CDP.
-
Environmental Management System
Hyosung TNC annually sets Key Performance Indicators (KPIs) and objectives for an environmental management items, including environmental qualifications management, environmental impact assessments, environmental compliance assessments, regulatory management, air and water pollutant discharge levels, waste generation, and stakeholder complaint responses. We establish the annual plans and monitor progress toward achieving these objectives.
Water Quality
Hyosung TNC minimizes unnecessary water consumption through close collaboration between production processes. Our Ulsan plant stores rainwater in on-site reservoirs for reuse as cooling water, while also recycling water used during operational processes to minimize water consumption. The Gumi plant releases primary treated wastewater to the Gumi City sewage treatment plant, where it is further treated and then supplied for reuse. By using retreated water, we prevent contamination of the Nakdong River and contribute to preventing water resource shortages.
Additionally, we have our own wastewater treatment facility to treat all wastewater generated in the manufacturing process, discharging it below legal contamination limits. Moreover, the Ulsan plant has installed a Total Monitoring System (TMS) to monitor water pollutant discharge in real time, while the Gumi plant commissions external measurement companies for water quality analysis every month, minimizing ecological damage to the Nakdong River basin.
Air Quality
Hyosung TNC periodically measures air pollutants to ensure compliance with legal emission standards. The Ulsan plant has installed TMS on major facilities to monitor air pollutant emissions in a real time, and we plan to expand TMS installation across the entire facility in the future.
Waste Management
Hyosung TNC makes multifaceted efforts to increase the recycling rate of waste materials. The Gumi plant incinerates waste in an external incinerator and reuses the generated steam in manufacturing processes. It also evaporates moisture from used liquid at the plant for reuse. The Ulsan plant recycles a majority of the wastewater previously sent to landfills and plans to continuously reduce wastewater generation by installing a high-efficiency dewatering machine.
Chemical materials
Hyosung TNC reports all chemical substances used to watershed and regional environmental agencies. Of these, information on hazardous substances is transparently disclosed to the public through the Chemical Substance Comprehensive Information System. Furthermore, we manage all chemicals used in our production processes through an ERP-based computer system. We only approve the purchase of materials after confirming our compliance with chemical substance regulations. For all purchased chemicals, we mandatorily provide Material Safety Data Sheets (MSDS) and ensure that they are readily available for employees to access. To enhance chemical substance management, we have developed a chemical accident prevention and management plan. Besides the annual legal regular inspections, our dedicated teams and environmental safety teams conduct weekly inspections of facilities handling hazardous chemicals.
Starting in 2016, our Gumi plant has formed a chemical safety community in partnership with the Daegu Regional Environmental Office for businesses handling hazardous chemicals. This initiative aims to prevent chemical accidents and respond swiftly in the event of an incident. Key activities include information exchange and collaboration among companies to establish an emergency response system through regular joint emergency drills. Similarly, our Ulsan plant has pledged to share information about chemical substance handling and collaborate with nearby companies in responding to chemical accidents. We are actively participating in the Ulsan Environment Engineers Association and the Gyeongnam Regional Joint Response Council for Chemical Accidents.
Zero-emission Vehicles
Hyosung TNC owns sustainable vehicles such as an electric cars that help to reduce air pollution and greenhouse gas emissions. We plan to gradually increase the proportion of zero-emission vehicles in our fleet.
Pollution Reduction Technology Development
-
Circluar technology to recycle abandoned resources
Development of carbon-reducing recycled fiber
Hyosung TNC is producing sustainable polyester yarn, called regen, through a groundbreaking technology that extracts useful components from discarded PET bottles. regen achieves a remarkable reduction in landfill waste and a decrease in carbon dioxide emissions.
Recycling approximately 866 500mL PET bottles for every ton of regen produced significantly minimizes the release of microplastics. Compared to conventional polyester products, regen offers approximately a 60% reduction in carbon dioxide emissions.
In efforts to address the issue of marine microplastics, Hyosung TNC has developed ocean-bound plastic (OBP) recycled polyester, becoming the first in Korea to obtain OBP certification.
-
Catalytic Technology as a substitute for Hazardous Chemicals
Application of Antimony-free product
Antimony-free is a catalyst based on tin, which is non-toxic to humans and the environment. Hyosung began developing this technology in 2017 and successfully completed its technical development in just three years, in 2020.
By utilizing the antimony-free catalyst, it is possible to replace harmful chemicals, such as antimony glycolate, used in the production of traditional nylon polyester. This substitution enhances the sustainability of the products. Moreover, the use of the antimony-free catalyst reduces the amount of catalyst input to 1/10 compared to before and also significantly decreases the amount of plastic waste generated during the polyester production process by over half compared to conventional catalysts.
Hyosung TNC is planning to apply the antimony-free catalyst to all polyester fiber manufacturing processes in the future and is currently conducting trial productions to proactively meet the sustainable fiber demands of major customers. Furthermore, we are working on patent registrations to expand the application of this technology in global markets, including the United States, China, Europe, and India.